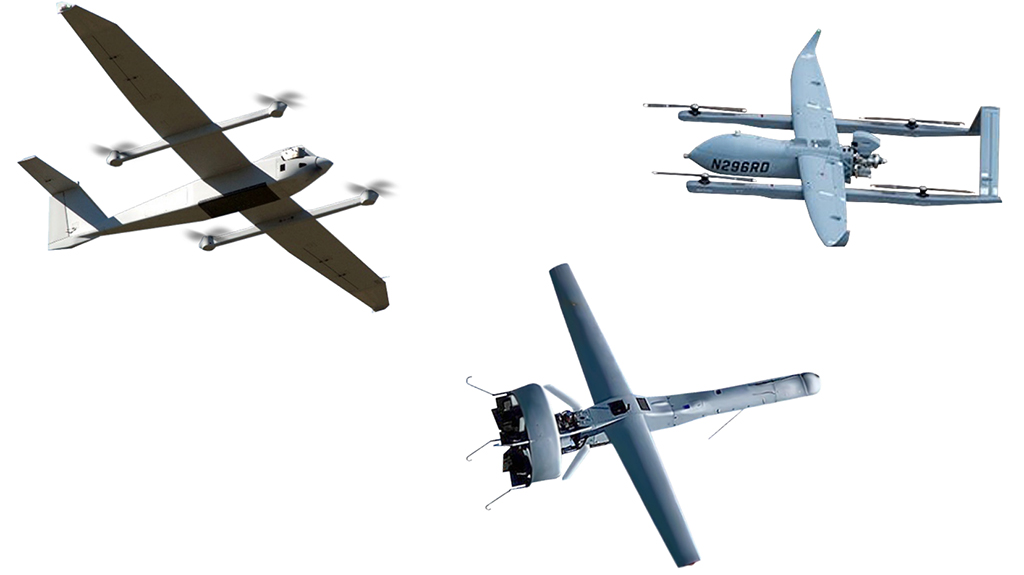
A team of University of North Texas College of Engineering researchers are helping make soldiers safer by improving the reliability of Army drone propulsion.
Most Army drones, also known as Unmanned Aerial Vehicles (UAV), are used for reconnaissance missions, but are often grounded because of accelerated wear and tear of engines from high altitude, high RPMs, extended missions and poor fuel quality available in areas of military operation.
“We have a big challenge facing us, since some components are lubricated by the fuel that they are delivering to the engine,” said Stephen Berkebile, tribological materials science tech area lead at the Army Research Laboratory. “That fuel can vary widely in its lubricating ability, so we need to look to other ways to ensure long component life.”
Materials scientists Diana Berman, Andrey Voevodin and Samir Aouadi are working to solve this problem with two parallel approaches – one geared toward improving the multi-fuel compatibility and the other focused on engine component endurance with protective surface coatings.
“We need to provide new materials and new processing technology to survive these conditions, and here at UNT, we’re uniquely fit for the task,” said Andrey Voevodin, associate dean for research. “We have a core of tribology experts, featuring several faculty members who are internationally recognized within the field.”
With the project, the UNT team is a part of a large U.S. Army Combat Capabilities Development Command Army Research Laboratory-led effort interfacing with a number of academia, national laboratories and industry experts to enhance the drone combustion engine versatility and reliability, researching ways to increase its reliability and make it compatible with different fuel types. It’s been designated as part of the Versatile Tactical Power and Propulsion Essential Research Program, requiring that a solution be provided to the Army within three years.
As one scientific breakthrough, the team is using catalytic conversion in protective coatings as a new concept for adapting surfaces that interact with lubrication. The effort includes creating a stronger and more robust surface while also making the surface self-adaptive, creating a way for the fuel to leave behind a protective and lubricating layer as it’s pumped to the engine.
“If we’re successful in these endeavors, it means more drones would be available in the field, providing soldiers with more data in real time, improving their awareness of the mission, and providing them an overall advantage in the battlefield with improved drone reliability, reach, survivability and lethality,” said Voevodin.